Man-made cellulosic fibres (MMCFs) are the second biggest group after cotton in the cellulose category and while they don’t rely on petrochemicals like the polyester and polyamide fibres, Viscose, which accounts for 91 per cent of the MMCF market, presents many challenges that we need to find solutions to in our pathway to a more sustainable textiles economy.
We look at the main challenges, solutions and some of the newest and promising cellulosic fibre options.
Challenges associated with Man-made cellulosic fibres
Deforestation & its environmental and social impacts
Sourcing the raw material for the production of MMCF is taxing on the environment: over 150 million trees are logged for man-made cellulose production every year and is on the upward trend, some of which are from sources that lack sustainable forestry management, sometimes even involving illegal trade. Illegal logging (for all wood products, texiles are among them) is in fact the most profitable natural resource crime, and accounts somewhere between 15 and 30 percent of global timber product trade. Illegal logging and the poor governance of the forest sector that often goes along with it have financial, ecological, and social costs to a society.
Chemical use, production methods & human labour rights
I put these two together because one of the greatest violation of human rights in the industry is the hazardous use of toxic chemicals. The production of traditional viscose for instance involves the use of carbon disulphide and sodium hydroxide (caustic soda) that have adverse health effects on people and wildlife. Consequences include neurological problems, birth defects and miscarriages among female workers or cancers like leukaemia, and ambient water and soil contamination from manufacturing discharges. Water usage varies depending on the process used but is generally on the high end for traditionally manufactured viscose compared to say synthetics (with higher water toxicity).
Traceability & Chain of Custody
Once cellulose has gone through the chemical transformation that turns it into a dissolving pulp for application, laboratory tests can’t identify where the cellulose was sourced from making it impossible to verify any sustainability claims. Hence it’s impossible to identify post-production the origins of the pulp unless it was documented at sources and the information is passed along the different stages and parties involved to maintain a Chain of Custody. Standards that are globally recognised include the Forest Stewardship Council (FSC) but no independent textile standard covering content claim assurance and environmental and social criteria for pulp and fibre processing.
Fortunately, the textile industry is making huge leaps in both using recycled content to reduce virgin cellulose sourcing, chemical and process enhancements to lower chemical toxicity levels and recover bi-products for reuse in the production stages, and lastly, with increasing systems and regulations for the traceability of raw materials.
Next Gen Solutions for MMCFs
Deforestation and chain of custody go together because even if a raw material was sustainabily sourced and certified as such, there needs to be a process in place for ensuring that the information gets passed on. According to Canopy, only 20 percent of Earth’s ancient forests remain large are in a healthy state that allows for the survival of biological diversity
Source certified only, not enough anymore
For a long time, globally recognised as one of the most reliable science-based labels, the Forest Stewardship Council (FSC) label issued by the FSC governing bodies to products that pass their on-the-ground audits was considered among the highest certifications for sustainability. It ensured chain of custody management, transparency of operations, protection of human rights (notably of the indigenous people who are often victims of the trade) and management, protection, of natural forested land. But we’re in 2021, and new tech is enabling us to step away from virgin raw material altogether.
Feedstock for cellulose that doesn’t use trees
Viscose producers looking to stand out from the crowd are jumping on the next-generation fibre that is using new technology. The new processes emerging are proving to be viable sources of low-energy, low-water and low-carbon emitting sources.
Nullarbor™ Fibre is the next tree-free fibre for real tree hugger | Source: nanollose.com
While some disruptive innovations are the fruit of cross-industry and brand partnerships (some major industry projects include the Full Circle Textiles Project: Scaling Innovations in Cellulosic Recycling, and the New Cotton Project), others are internally developed by leaders in regenerated fibre technologies. First Lenzing (2017) and then Aditya Birla and Tangshan Sanyou (2019) have already begun the transition to Next-Gen feedstock from waste materials. Here’s a quick run through the op technology and sustainability ranking materials in this fibre group. We’ ve picked out a few of the newest and most sustainable cellulosic fibres:
Top New-Gen regenerated cellulosic fibres shifting the industry
1. Lenzing’s TENCEL™ fibre with REFIBRA™ technology are an enhanced version of their standard TENCEL™ Lyocell fibre. It uses up to one third of regenerated pulp obtained through REFIBRA™ technology which is added to sustainably sourced virgin wood pulp in order to obtain new TENCEL™ Lyocell fibres.
Benefits: reduced use of the virgin wood pulp by adding upcyclined material to their fibre mix + removing the use of caustic soda in the lyocell process + closed loop production process (as per their standard TENCEL™ Lyocell fibre).
Traceability: TENCEL™ fibre with REFIBRA™ technology are identifiable in yarns, fabrics and final garments owing to the innovative special identification technology designed to confirm fiber origin. In turn, this improves supply chain transparency.
2.Aditya Birla Group’s Birla Cellulose excels in sustainable forestry: the pulp used is guaranteed 100 percent compliant to FSC®, SFI® or PEFC™ Standards.
Benefits: sustainable educed use of the virgin wood pulp by adding upcyclined material to their fibre mix + removing the use of caustic soda in the lyocell process + closed loop production process (as per their standard TENCEL™ Lyocell fibre).
Traceability: All of the sourcing sites are FSC® CoC (Chain of Custody) certified. The company uses blockchain traceability platform GreenTrack™ to provide “ forest to fashion transparency”, and ranks number 1 in Canopy’s Hot Button report 2020.
3.Re:newcell’s Circulose® hit the high street in spring last year offering H&&M customers a dress made in part from regenerated cellulosic fibre. The technology provides a dissolving pulp for the use of creating MMCFs that are as good quality as those made from virgin wood and plant sourced pulp.
Benefits: no trees needed + on par quality to virgin-sourced dissolving + reduce waste from textiles + uses renewable energy
Traceability: no information
4.Nullarbor Fibre made from Nanollose, a microbial cellulose grown in a lab within 10 to 15 days using feedstock of liquid organic wastes from the food and beverage industries.
Benefits: 100% geographic freedom from water sources + unbeatable field to yield capacity + fast production (can be produced within 10 to 15 days) + utilizes waste resources.
Traceability: no information
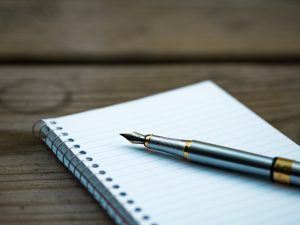
Author
Related Courses
Fashion Design & Product Development
- 12 hours + 3 hrs for Assessment
- Intermediate
- English